常见冲压件的质量问题及解决办法分析
文章来源:本站 发布时间:2020-11-03 09:26:10
一、冲裁件的常见缺陷及原因分析
冲裁是利用模具使板料分离的冲压工序。
冲裁件常见缺陷有:毛刺、制件表面翘曲、尺寸超差。
1、毛刺
在板料冲裁中,产生不同程度的毛刺,一般来讲是很难避免的,但是提高制件的工艺性,改善冲压条件,就能减小毛刺。
产生毛刺的原因主要有以下几方面:
1.1 间隙
冲裁间隙过大、过小或不均匀均可产生毛刺。影响间隙过大、过小或不均匀的有如下因素:
a. 模具制造误差-冲模零件加工不符合图纸、底板平行度不好等;
b. 模具装配误差-导向部分间隙大、凸凹模装配不同心等;
c. 压力机精度差—如压力机导轨间隙过大,滑块底面与工作台表面的平行度不好,或是滑块行程与压力机台面的垂直度不好,工作台刚性差,在冲裁时产生挠度,均能引起间隙的变化;
d. 安装误差—如冲模上下底板表面在安装时未擦干净或对大型冲模上模的紧固方法不当,冲模上下模安装不同心(尤其是无导柱模)而引起工作部分倾斜;
e. 冲模结构不合理-冲模及工作部分刚度不够,冲裁力不平衡等;
d. 钢板的瓢曲度大-钢板不平。
1.2 刀口钝
刃口磨损变钝或啃伤均能产生毛刺。
影响刃口变钝的因素有:
a.模具凸、凹模的材质及其表面处理状态不良,耐磨性差;
b.冲模结构不良,刚性差,造成啃伤;
c. 操作时不及时润滑,磨损快;
d.没有及时磨锋刃口。
1.3 冲裁状态不当
如毛坯(包括中间制件)与凸模或凹模接触不好,在定位相对高度不当的修边冲孔时,也会由于制件高度低于定位相对高度,在冲裁过程中制件形状与刃口形状不服帖而产生毛刺。
1.4 模具结构不当。
1.5 材料不符工艺规定
材料厚度严重超差或用错料(如钢号不对)引起相对间隙不合理而使制件产生毛刺。
1.6 制件的工艺性差
形状复杂有凸出或凹入的尖角均易因磨损过快而产生毛刺。
毛刺的产生,不仅使冲裁以后的变形工序由于产生应力集中而容易开裂,同时也给后续工序毛坯的分层带来困难。大的毛刺容易把手划伤;焊接时两张钢板接合不好,易焊穿,焊不牢;铆接时则易产生铆接间隙或引起铆裂。因此,出现允许范围以外的毛刺是极其有害的。对已经产生的毛刺可用锉削、滚光、电解、化学处理等方法来消除。
2、制件翘曲不平
材料在与凸模、凹模接触的瞬间首先要拉伸弯曲,然后剪断、撕裂。由于拉深、弯曲、横向挤压各种力的作用,使制件展料出现波浪形状,制件因而产生翘曲。
制件翘曲产生的原因有以下几个方面:
2.1 冲裁间隙大
间隙过大,则在冲裁过程中,制件的拉伸、弯曲力大,易产生翘曲。改善的办法可在冲裁时用凸模和压料板紧紧地压住,以及保持锋利的刃口,都能受到良好的效果。
2.2 凹模洞口有反锥
制件在通过尺寸小的部位时,外周就要向中心压缩,从而产生弯曲。
2.3 制件结构形状产生的翘曲
制件形状复杂时,制件周围的剪切力就不均匀,因此产生了由周围向中心的力,使制件出现翘曲。解决的办法就是增大压料力。
2.4 材料内部应力产生的翘曲
材料在轧制卷绕时产生的内部应力,在冲裁后移到表面,制件将出现翘曲。解决的方法时开卷时通过矫平机矫平。
2.5 由于油、空气和接触不良产生的翘曲
在冲模和制件、制件和制件之间有油、空气等压迫制件时,制件将产生翘曲,特别是薄料、软材料更易产生。但如均匀的涂油、设置排气孔,可以消除翘曲现象。制件和冲模之间表面有杂物也易在、使制件产生翘曲。
冲裁时接触面不良也会产生翘曲。
3、尺寸精度超差
3.1 模具刃口尺寸制造超差
3.2 冲裁过程中的回弹、上道工序的制件形状与下道工序模具工作部分的支承面形状不一致,使制件在冲裁过程中发生变形,冲裁完毕后产生弹性回复,因而影响尺寸精度。
3.3 板形不好。
3.4 多工序的制件由于上道工序调整不当或圆角磨损,破坏了变形时体积均等的原则,引起了冲裁后尺寸的变化。
3.5 由于操作时定位不好,或者定位机构设计得不好,冲裁过程中毛坯发生了窜动。或者由于剪切件的缺陷(棱形度、缺边等)而引起定位的不准,均能引起尺寸超差。
3.6 冲裁顺序不对。
二、弯曲件的常见缺陷及原因分析
弯曲件常见缺陷有:形状与尺寸不符、弯裂、表面擦伤、挠度和扭曲等。
1、形状与尺寸不符
主要原因是会弹和定位不当所致。解决的办法除采取措施以减少回弹外,提高毛坯定位的可靠性也是很重要的,通常采用以下两种措施;
1.1 压紧毛坯
采用气垫、橡皮或弹簧产生压紧力,在弯曲开始前就把板料压紧。为达到此目的,压料板或压料杆的顶出高度应做得比凹模平面稍高一些。
1.2 可靠的定位方法
毛坯的定位形式主要有以外形为基准和以孔为基准两种。外形定位操作方便,但定位准确性较差。孔定位方式操作不大方便,使用范围较窄,但定位准确可靠。在特定的条件下,有时用外形初定位,大致使毛坯控制在一定范围内,更后以孔位更后定位,吸取两者的优点,使之定位即准确又操作方便。
2.弯曲裂纹
影响裂纹产生的因素是多方面的,主要有以下几个方面:
2.1 材料塑性差。
2.2弯曲线与板料轧纹方向夹角不符合规定:排样时,单向V形弯曲时,弯曲线应垂直于轧纹方向;双向弯曲时,弯曲线与轧纹方向更好成45度。
2.3弯曲半径过小。
2.4 毛坯剪切和冲裁断面质量差——毛刺、裂纹。
2.5 凸凹模圆角半径磨损或间隙过小——进料阻力增大。
2.6 润滑不够——摩擦力较大
2.7 料厚尺寸严重超差——进料困难
2.8 酸洗质量差
3、表面擦(拉)伤
表面擦伤的主要原因是模具工作部分选材不当,热处理硬度低,凹模圆角磨损、光洁度差,弯曲毛坯表面质量差(有锈、结疤等),材料厚度超差,工艺方案选择不合理,缺少润滑等。
三、大型曲面拉深件的常见缺陷及原因分析
1、大型曲面制件的拉深特点
1.1 变形特点
大型曲面制件的变形特点是:周边为拉深,内部则有胀形成分。表面形状是靠压料面外部材料来补充,而内部则靠材料延伸来满足胀形的要求。同时由于拉深深度不一,形状复杂,变形部分周边分布不均。因此,控制材料的流向及流速极为重要。大型曲面制件的局部既易起皱,又易开裂。
1.2 要有足够稳定的压边力
大型曲面制件不仅要求一定的拉深力,而且要求在其拉深过程中具有足够的稳定的压边力。此类制件往往是轮廓尺寸较大,深度较深的空间曲面,所以需用变形力和压边力都较大。在普通带气垫的单动压力机上,压边力只有名义吨位的1/6左右,而且压边力也不稳定,难以满足此类制件的工艺要求,因此在大量生产中,此类制件的拉深均在双动压力机上进行。双动压力机具有拉深和压边的两个滑块,即内滑块和外滑块,压边力可达到总拉深力的40%-50%以上,能满足制件周边变形分布不均的要求,且压边力稳定,易得到刚度较好的拉深件。
1.3 拉深件必须有足够的刚度
此类制件大多是作为机械的外壳,要求有足够的刚度(使用中不会发生颤抖和噪音)和尺寸稳定性(保证焊接、装配质量)。这就要求在拉深过程中使材料各部位受到均匀的拉应力(更理想的是双向拉应力状态),且使拉应力超过屈服极限,而低于强度极限,使制件的弹性回复减少到更低限度,使形状不致于产生畸变,同时也不致于破裂。
2、常见缺陷及原因分析
大型曲面拉深件常见的缺陷有:裂纹和破裂、皱纹和折纹、棱线不清、刚度差、表面划痕、表面粗糙和滑移线等。
2.1 裂纹和破裂
裂纹和破裂产生的原因主要是由于局部毛坯受到的拉应力超过了强度极限所致。具体影响的原因有:
2.1.1材料的冲压性能不符合工艺要求。
2.1.2板料厚度超差-当板料厚度超过上偏差时,局部间隙小的区域进料时卡死,冲压变形困难,材料不易通过该处凹模内而被拉断。当板料厚度超过下偏差时,材料变薄了,横剖面单位面积上的压应力增大,或者由于材料变薄,阻力减小,流入凹模内的板料过多而先形成皱纹,这时,材料不易流动而被拉裂。
2.1.3材料表面质量差-划痕引起应力集中、锈蚀增大后阻力。
2.1.4压料面的进料阻力过大-毛坯外形大、压料筋槽间隙小、凹模圆角半径过小、外滑块调的过深、拉深筋过高、压料面和凹模圆角半径光洁度差。
2.1.5局部拉深量太大,拉深变形超过了材料变形极限。
2.1.6在操作中,把毛坯放偏,造成一边压料过大,一边压料过小。过大的一边则进料困难,造成开裂;过小的一边,进料过多,易起皱,皱后进料困难,引起破裂。
2.1.7不按工艺规定涂润滑剂,后阻力增大,造成进料困难而开裂。
2.1.8冲模安装不当或压力机精度差,引起间隙偏斜,造成进料阻力不均。
2.2 皱纹和折纹
皱纹产生的原因主要因为局部毛坯受压引起失稳和材料流向不均引起局部材料堆积而产生皱纹。具体有下面几个方面:
2.2.1制件的冲压工艺性差,冲压方向和压料面形状确定不当,很难控制材料的流动速度,引起皱纹。
2.2.2压料面的进料阻力太小,进料过多而起皱。这时可调节外滑块压力或改变拉深毛坯局部形状,增加压料面积来消除,或局部增加拉深筋来增大进料阻力。
2.2.3压料面接触不好,严重时形成里松外紧。材料通过外紧区域后压料圈就失去压料作用,造成进料过多,产生皱纹。这时要重新研磨压料面,保证全面接触,允许稍有里紧外松。
2.2.4涂油润滑过多。
2.2.5外滑块调整不当,造成倾斜,使各处压料面压力不均,松的地方易起皱。
2.3 棱线不清
制件从外表观察,要求棱线清晰。如果压力机的压力不够,则在拉深成形中,在材料变形过程终止时,得不到足够墩死的压力,则棱线不清。另外,冲模的导向不好,工作部分间隙不均匀,或凸模及凹模安装不正确(倾斜),压机的平行度不好也能引起棱线不清。
2.4 刚性差
形成刚性差的主要原因除制件工艺性不好外,主要的则是压料面的进料阻力太小,材料塑性变形不够引起的。此时可考虑增加拉深筋或将圆式拉深筋改为坎式拉深筋,以增大进料阻力。这也是单动压力机拉深出来的制件的刚度比双动压力机拉深出来的制件差的原因。
2.5 表面划痕(拉伤)
表面划痕通常有如下原因造成:凹模圆角部分光洁度不够,这样在拉深过程中材料被划伤,并有可能使材料粘附在凹模上,而形成划痕;由于脏物落入凹模中或拉深油不干净,也会划伤制件表面;如果压料面是由镶块组成的,则由于镶块结合不好,也会造成划痕;由于工艺补充部分过小,通过凹模口的划痕没有被切去。
2.6 表面粗糙和滑移线
表面粗糙的缺陷是材料本身晶粒度过大引起的。
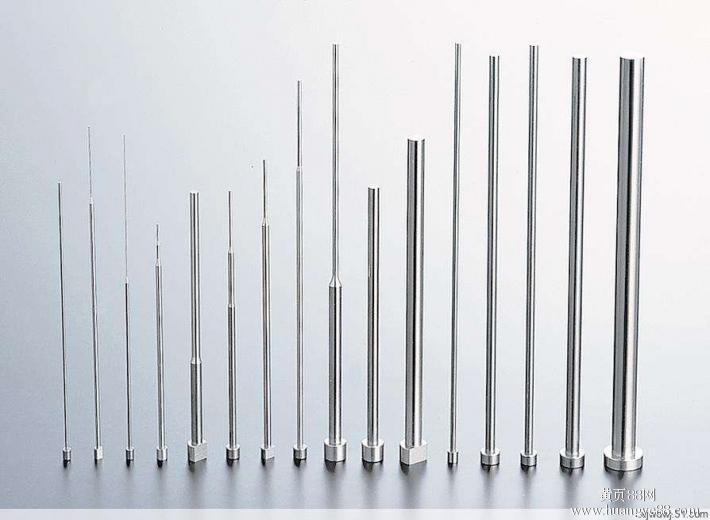
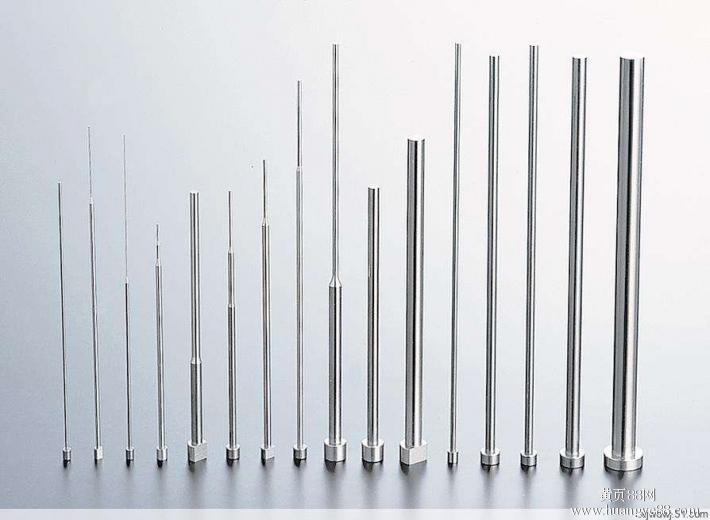
本文部分内容来源于网络,我们仅作为信息分享。本站仅提供信息存储空间服务,不拥有所有权,不承担相关法律责任。如发现本站有涉嫌抄袭侵权/违法违规的内容, 请发送邮件至 promaxsts@163.com 举报,一经查实,本站将立刻删除。
上一篇:skd11更新优惠价格 下一篇:skd11机械性能怎么样?